Champlain Prototype is a design and manufacturing company. We specialize in prototypes and custom replacement parts.
Recent Work
Flair Pro 2 Mechanism Conversion
You could call me a coffee enthusiast. I enjoy brewing with many methods, one of my favorites being espresso. I first started making espresso with a Flair lever espresso press. If you’re unfamiliar with the process, coffee grounds and hot water are put in the device, and a lever is used to generate pressure on the water which is forced through the grounds.
This works, and Flair makes a good machine at a reasonable price point. There is always room for improvement, though.
The primary issue I have with it is that the lever doesn’t give the mechanical advantage that I think is necessary. In other words, you have to push very hard to brew your coffee. You may notice in the photo of the unmodified version the person using two hands. That is necessary.
The second issue I have with it is this. Once finished brewing, you’ll lift the lever to depressurize the chamber and stop the brew process. There will be excess water in the chamber, near boiling. This extra water will be pressurized and will push either the plunger or brew chamber up. By design the plunger is supposed to move up for depressurization. If, however, the brew chamber moves up, the entire contents of the chamber will be emptied on your coffee, hands, and counter. Very frustrating.
Design time: 7 hours
Manufacturing time: 3 hours
Custom Chainring
Vermont is a great state for mountain biking. Trails are often steep, and I find myself using the lowest end of my gearing often. To ease the effort it takes to climb, a simple solution is to decrease the size of the front “sprocket” (chainring). Unfortunately, the OEM for my drivetrain doesn’t offer smaller chainrings. There are few options aftermarket, and at the time of this project the one I wanted was out of stock.
A bit of reverse-engineering, some prototyping, and finally some machining, I had what I wanted.
I have put many miles on this initial design (multiple years of riding) and, aside from some wear, it works well. 7075 aluminum was originally chosen for strength and machinability, but I am in the process of taking the design to a hardened stainless steel. This will provide better wear resistance than any commercially available, anodized-aluminum chainring.
Design time: 5 hours
Manufacturing time: 4 hours
Prototype Adjustable Stem
Another mountain biking project, this one is a proof of concept. To explain the problem simply, bicycles have different geometries for different riding conditions. “Downhill” mountain bikes have very tall handlebars. This is because when the bike is pointed down a steep hill, you want your handlebars to be set higher, else your weight is too far forward (less stable). When climbing steep hills, however, you’d really prefer the handlebars to be lower. Having them set too high will shift your weight to the rear wheel, unload the front wheel, and make steering very difficult.
In my mind the solution is simple: an adjustable “stem”, the part that the handlebars attach too.
Now, adjustable stems have been around for decades, but their adjustability is severely limited. I wanted to be able to set my handlebars lower than anything on the market, while also being able to set them as high as a “downhill” bike.
A few measurements, a couple hours in Solidworks, some flying chips, and I had a testable prototype.
I have been running this setup for over a year now and the benefits are clear. The next step is to improve the adjustment mechanism as well as address some flaws in the initial prototype.
Design time: 2 hours
Manufacturing time: 3 hours
Missing Part for Menorah
This design project required replacing the missing center candle holder, called the “Shamash”. A design was generated in CAD, then a prototype was printed to evaluate fit and aesthetics. Once a final design was conceived, a manufacturing process was chosen to create the part. Lost wax casting was chosen as an economical process that would result in an excellent surface finish.
It is a process not available in-house, but an appropriate vendor was identified. Once the part was received all parts were buffed to give a uniform, polished finish.
Design time: 3 hours
Final fit & finish: 1 hour
Custom Riveter Jaws
This project involved creating a replacement set of jaws for a riveting tool. This tool compresses a solid rivet in a hole to create a secure connection. For a specific job, however, the jaw reach was not enough to reach the rivet. I designed these jaws that give more reach, more leverage, and more clearance over the original design. A proper, hardened steel was chosen for strength and durability.
Design time: 2 hours
Manufacturing time: 4 hours
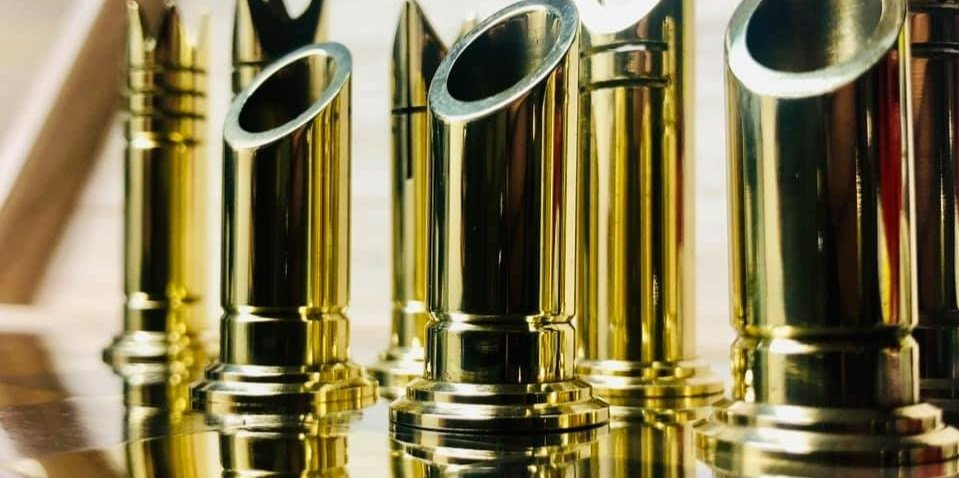